How are toilets produced in Corraveni?
A ceramic toilet for dealing with excrement is necessary in every home and bathroom. People in different countries may use different types of toilets. European families prefer two-piece (close-coupled) water closet, usually of washdown flushing featured with bigger sized trapway. The washdown two-piece toilets are usually flushed through water gravity. Outer diameter of the trayway is around 100mm. American families prefer one-piece toilet, usually of siphonic flushing featured with smaller sized trapway. The siphonic toilets are usually flushed through siohon function of the tube. Outer diameter of the trapway will be smaller than washdown toilet.
There are also many other toilet variants such as wall-hung toilet, which usually comes with a concealed cistern and metal frame. Back-to-Wall toilets are also very popular in Europe. It makes the bathroom very modern and clean with the concealed installation system.
But how are ceramic toilets made in Corraveni? What’s the process? Here we’ll give an overview of how they are produced in ceramic toilet manufacturers in China.
Raw Material Preparation
Toilet bowls and cisterns are made from a special clay called vitreous china, which is a composite raw material. It’s a mix of several kinds of clay, called ball clay and china clay, silica, and a fluxing agent. Quartz and feldspar are also commonly used.. Hard material as quartz and feldspar usually act as bones of a toilet body, it forms the main structure of the toilet. Ball clays and china clay act as shaping material, which helps to form the shape of the toilet.
After being moved from outside to ceramic toilet factory, the raw material will be mixed according to Corraveni’s specific formula and proportion. They’ll be mixed and grinded in big ball mills into slurry slips. Workers at the toilet factory will then first thin the slurry slip to a watery consistency. Then, they will feed it through very fine screens in order to sieve out any impurities. A big magnet may also be used to remove the iron dust. (the iron dust easily bring defects on ceramic surface) The purified slip is thickened again, and pumped into storage tanks in preparation for use in toilet casting. (The purified will be stored there for several days so that it can be more stable. Duing the process, QC from Corraveni will keep a dynamic monitoring of the clay. They’ll take samples and test the chemical and physical performance according to our quality standard.
Casting Process
Next, the slip is carried through tubes and pumps into the toilet casting lines.
Most toilet manufacturers in China have 2 kinds of casting lines: One is normal standard casting lines. The other is most advanced high-pressure automatic casting machines.
Taking normal standard casting lines as example, workers will fill the plaster molds with the slip. The molds are in the shape of the desired toilet piece, except they are about 12-14% bigger, to allow for shrinkage. The casting workers fill the molds completely with the slip, and let it sit there for about an hour. Then, the workers will drain out any excess slip. The drained slip will be recycled for later use. The clay sits in the mold for another few hours. The plaster of Paris absorbs water from the clay, and the clay dries to the point where the mold can be safely removed. At this point, the casting is semisolid, and is called greenware. Workers use hand tools and sponges to smooth the edges of the casting and to make holes for drains and fittings.
Greenware maintenance
The greenware castings are left to dry in the open air for some time. During the drying process, the workers will keeping monitoring the greenware and wet the surface with sponge to avoid cracks. Then they are put into a dryer for 20 hours. Through the process, The toilet bases are cast from a slurry of vitreous china and molded into the base shape. Once molded, the greenware, as it is called, goes through a series of drying, glazing, and firing steps until it reaches final inspection process.
To avoid defected products, Corraveni will arrange a during-process quality checking to the greenware. QC will check each greenware carefully, qualified greenware will be sent to the next process and wrong greenware will be returned or recycled according to Corraveni’s internal quality control standard.
The recycle system is able to recycle much of its clay. As long as it has not been fired, all the clay is reusable. Even the air-dried greenware can be scrapped, softened and reprocessed into the watery slip. (actually, even fired pieces can now be recycled and mixed into the raw material, which will improve the performance and stability of the raw material)
Glazing
The dryer is usually set to 200° F (93° C). Most drying rooms in China toilet factory are positioned next to the kiln, so that to utilize the excess heat of the kiln. After the castings come out of the dryer, they have lost all but about 0.5% of their moisture. At this point workers spray the greenware castings with glaze. Glaze is a shiny, waterproof coating comes from quartz and feldspar. Wokers will spray the glaze onto the greenware with a sprayer. Corraveni bath uses spraying robots to spray the glaze usually.
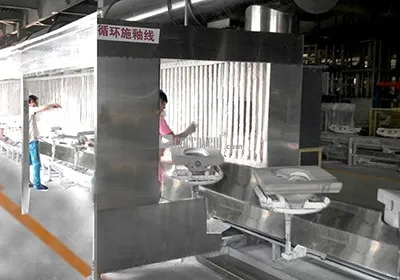
Firing
After the glazing process, the toilet pieces are ready for burning in the kiln.
The kilns at a large ceramic sanitary ware factory are the most important equipment. Shuttle kiln and tunnel kiln are commonly used kilns in China. Shuttle kiln is flexible for toilet production at different quantity. Tunnel kiln is suitable for scale production with lower energy cost, but the kiln should keep running. More and more China factories are turning to shuttle kilns now. Corraveni are using both types of kilns.
The ready for burning toilet will move through the kiln on a conveyance called a car. Each car is loaded with a number of toilet pieces on the silicon boards, and then it moves automatically through the hot kiln at a very slow pace. Because rapid changes in temperature will cause the clay to crack, the cars move leisurely through graduated temperature zones: the first zone is about 400° F (204° C), and it increases in the middle of the kiln to over 2,200° F (1,204° C) degrees. The temperature gradually decreases from there, so that the final temperature is only about 200° F (93° C). The whole firing process takes approximately 24-40 hours.(It depends on the configurations of the kilns. This process applies only to tunnel kilns)
Quality Inspection
When the toilet pieces are removed from the kiln and fully cool, they are ready for inspection. As with any industrial process, quality monitoring and checks are taken at several points in the manufacturing process of ceramic toilets. The clay is sieved and purified before it is pumped into the factory's tanks. Workers doing the manual finishing of the castings check the pieces for cracks or deformities. After firing, each toilet is tested individually. Corraveni QC will check the appearance quality, machining precision and final step to check the function.
Each toilet piece must be inspected for cracks. There are several ways to do this. One is to fill water into the pan and put the pan there for 6-24 hours to check whether leakage exists. The other way is to use a machine called air leakage detector, which is more precise and much quicker (around 20-30 seconds)
After inspection, There is the packaging process. Workers will pack the toilets into cartons , with the flushing mechanism, toilet seat cover or other assigned plumbing accessories from the buyer.